Weld Defect atau Cacat las adalah hasil pengelasan yang tidak memenuhi syarat keberterimaan yang sudah dituliskan di standart (ASME IX, AWS, API, ASTM). Penyebab cacat las dapat dikarenakan adanya prosedur pengelasan yang salah, persiapan yang kurang dan juga dapat disebabkan oleh peralatan serta consumable yang tidak sesuai standart.
Jenis cacat las pada pengelasan ada beberapa tipe yaitu cacat las internal (berada di dalam hasil lasan) dan cacat las visual (dapat dilihat dengan mata). Jika kita ingin mengetahui defect atau cacat pengelasan internal maka kamu memerlukan alat uji seperti Ultrasonic Test dan Radiography Test untuk pengujian yang tidak merusak, sedangkan untuk uji merusak kamu dapat menggunakan uji Bending atau makro. Untuk jenis jenis cacat pengelasan visual atau surface Anda dapat menggunakan pengujian Penetrant Test, Magnetic Test atau kaca pembesar.
Cacat Las Undercut
Undercut adalah sebuah cacat las yang berada di bagian permukaan atau akar, bentuk cacat ini seperti cerukan yang terjadi pada base metal atau logam induk. Jenis cacat pengelasan ini dapat terjadi pada semua sambungan las, baik fillet, butt, lap, corner dan edge joint.
Penyebab Cacat Las Undercut:
• Arus pengelasan yang digunakan terlalu besar.
• Travel speed / kecepatan las terlalu tinggi.
• Panjang busur las terlalu tinggi.
• Posisi elektroda kurang tepat.
• Ayunan tangan kurang merata, waktu ayunan pada saat disamping terlalu cepat.
Cara mencegah Cacat Undercut:
• Menyesuaikan arus pengelasan, Anda dapat melihat ampere yang direkomendasikan di bungkus elektroda atau wps (Welding Procedure Specification).
• Kecepatan las diturunkan.
• Panjang busur diperpendek atau setinggi 1,5 x diameter elektroda.
• Sudut kemiringan 70-80 derajat (menyesuaikan posisi).
• Lebih sering berlatih untuk mengayunkan yang sesuai dengan kemampuan.
Porosity (Porositas)
Cacat Porositas adalah sebuah cacat pengelasan yang berupa sebuah lubang lubang kecil pada weld metal (logam las), dapat berada pada permukaan maupun didalamnya. Porosity ini mempunyai beberapa tipe yaitu Cluster Porosity, Blow Hole dan Gas Pore.
Penyebab Cacat Las Porositas:
• Elektroda yang digunakan masih lembab atau terkena air.
• Busur las terlalu panjang.
• Arus pengelasan terlalu rendah.
• Travel Speed terlalu tinggi.
• Adanya zat pengotor pada benda kerja (karat, minyak, air dll).
• Gas Hidrogen tercipta karena panas las.
Cara Mengatasi Cacat Las Porositas:
• Pastikan elektroda yang digunakan sudah dioven (jika disyaratkan), jangan sampai kawat las terkena air atau lembab.
• Atur tinggi busur kurang lebih 1,5 x diameter kawat las.
• Ampere disesuaikan dengan prosedur atau rekomendasi dari produsen elektroda.
• Persiapan pengelasan yang benar, memastikan tidak ada pengotor dalam benda kerja.
• Untuk material tertentu panas tidak boleh terlalu tinggi, sehingga perlu perlakukan panas.
Slag Inclusion
Welding Defect Slag Inclusion adalah cacat yang terjadi pada daerah dalam hasil lasan. Cacat ini berupa slag (flux yang mencair) yang berada dalam lasan, yang sering terjadi pada daerah stop and run (awal dan berhentinya proses pengelasan). Untuk melihat cacat ini kita harus melakukan pengujian radiografi atau bending.
Penyebab Cacat Las Slag Inclusion:
• Proses pembersihan Slag kurang, sehingga tertumpuk oleh lasan.
• Ampere terlalu rendah.
• Busur las terlalu jauh.
• Sudut pengelasan salah.
• Sudut kampuh terlalu kecil.
Cara Mencegah Cacat Slag Inclusion:
• Pastikan lasan benar benar berseih dari slag sebelum mengelas ulang.
• Ampere disesuaikan dengan prosedur.
• Busur las disesuaikan.
• Sudut pengelasan harus sesuai.
• Sudut kampuh lebih dibesarkan (50-70 derajat).
Tungsten Inclusion
Cacat las Tungsten Inclusion adalah cacat pengelasan yang diakibatkan oleh mencairnya tungsten pada saat proses pengelasan yang kemudian melebur menjadi satu dengan weld metal, cacat ini hampir sama dengan slag inclusion namun saat diuji radiografi tungsten inclusion berwana sangat terang. Untuk jenis cacat las ini hanya terjadi pada proses pengelasan GTAW.
Penyebab Tungsten Inclusion:
• Tungsten sudah tumpul saat proses pengelasan.
• Jarak tungsten terlalu dekat.
• Ampere terlalu tinggi.
Cara Mengatasi Cacat Las Tungsten Inclusion:
• Tungsten harus diruncingkan sebelum digunakan untuk mengelas.
• Jarak harus disesuaikan.
• Ampere mengikuti range yang ada di prosedur.
Incomplete Penetration
Incomplete Penetration (IP) adalah sebuah cacat pengelasan yang terjadi pada daerah root atau akar las, sebuah pengelasan dikatakan IP jika pengelasan pada daerah root tidak tembus atau reinforcemen pada akar las berbentuk cekung.
Penyebab Cacat Incomplete Penetration:
• Travel speed terlalu tinggi.
• Jarak gap atau root opening terlalu lebar.
• Jarak elektroda atau busur las terlalu tinggi.
• Sudut elektroda yang salah.
• Ampere las terlalu kecil.
Cara mencegah cacat Incomplete Penetration:
• Travel speed disesuaikan dengan WPS.
• Standar gap atau root opening 2-4 mm.
• Standar jarak elektroda 1,5 x diameter elektroda.
• Ampere disesuaikan dengan Welding Prosedur.
Incomplete Fusion
Cacat Incomplete Fusion adalah sebuah hasil pengelasan yang tidak dikehendaki karena ketidaksempurnaan proses penyambungan antara logam las dan logam induk. Cacat ini biasanya terjadi pada bagian samping lasan.
Penyebab Cacat Incomplete Fusion:
• Posisi Sudut kawat las salah.
• Ampere terlalu rendah.
• Sudut kampuh terlalu kecil.
• Permukaan kampuh terdapat kotoran.
• Travel Speed terlalu tinggi.
Cara Mengatasi Cacat Incomplete Fusion:
• Memperbaiki Posisi Sudut Elektroda.
• Menaikkan Ampere sesuai dengan WPS atau Ampere Recomended.
• Sudut kampuh sesuai dengan yang di WPS.
• Melakukan persiapan pengelasan yang benar, membersihkan semua kotoran.
• Mengatur Travel Speed yang sesuai.
Over Spatter
Spatter adalah percikan las, sebenarnya jika spater dapat dibersihkan maka tidak termasuk cacat. Namun jika jumlahnya berlebih dan tidak dapat dibersihkan maka dikategorikan dalam cacat visual.
Penyebab Spater atau percikan las berlebih:
• Ampere terlalu tinggi.
• Jarak elektroda dengan base metal terlalu jauh.
• Elektroda lembab
Cara mencegah terjadinya cacat pengelasan Over Spatter:
• Arus diturunkan sesuai dengan rekomendasi.
• Panjang busur ( 1,5 x diameter Elektroda ).
• Elektroda dioven sesuai dengan handbook (khususnya kawat las low hidrogen).
Hot Crack
Hot Crack (retak panas) adalah sebuah retak pada pengelasan dimana retak itu terjadi setelah proses pengelasan selesai atau saat proses pemadatan logam lasan.
Penyebab Hot Crack:
• Pemilihan elektroda yang salah.
• Tidak melakukan perlakuan panas.
Cara Mencegah Hot Crack:
• Menggunakan elektroda yang sesuai dengan WPS atau Low Hidrogen yang mempunyai sifat regangan yang tinggi.
• Melakukan perlakuan panas (PWHT dan Preheat)
Cold Cracking.
Cold Cracking (retak dingin) adalah sebuah retak yang terjadi pada daerah lasan setelah beberapa waktu (memerlukan waktu, bisa 1 menit, 1 jam, atau 1 hari) proses pengelasan selesai.
Penyebab Cold Cracking atau Retak dingin:
• Retak Dingin pada Bahan Las (Cold Cracking).
• Cooling Rate terlalu cepat.
• Arus pengelasan terlalu rendah.
• Travel speed terlalu tinggi.
• Tidak dilakukan pemanasan awal (pre heat).
Cara mencegah terjadinya Cold Cracking:
• Perlambat pendinginan setelah proses pengelasan.
• Panas yang diterima sesuaikan dengan WPS.
• Gunakan Arus yang direkomendasi.
• Travel speed pengelasan tidak terlalu cepat (lihat wps yang ada).
• Lakukan pre heat (untuk material yang karbon ekuivalen diatas 0,40 maka harus dipreheat).
Distorsi
Pengertian distorsi pada pengelasan adalah sebuah perubahan bentuk material yang diakibatkan panas yang berlebih saat proses pengelasan berlangsung. Distorsi ini terjadi saat proses pendinginan, karena adanya panas yang berlebih maka material dapat mengalami penyusutan atau pengembangan sehingga akan tarik menarik dan membuat material tersebut melengkung.
Penyebab terjadinya distorsi:
• Panas yang berlebih.
• Ampere terlalu tinggi.
• Take weld (las ikat) kurang kuat.
• Persiapan pengelasan yang salah.
Cara mencegah distorsi las:
• Menyesuaikan arus dengan yang ada di WPS.
• Take weld (las ikat) ditambah atau memberikan stopper (penguat pada logam induk).
• Melakukan Persiapan pengelasan yang benar.
Jenis jenis cacat pengelasan dan penyebabnya di atas dapat terjadi pada las listrik (SMAW), GMAW, GTAW, SAW, FCAW, OAW. Namun untuk tungsten inclusion hanya terjadi pada GTAW, karena hanya pengelasan tersebut yang menggunakan logam tungsten.
Cacat Non Visual dan Visual
Cacat non visual terbagi atas : root porosity, root concavity, root cracks, blow hole, incomplete pene-tration, excessive penetration, excess wire, root undercut, root underfill. Sedangkan cacat las visual terbagi atas : spatters, surface porosity, pin hole, surface cracks, surface cold lap, surface concavity, surface undercut, surface underfill, excessive reinforce ment, wide bead, stop start dan high low.
Root Concavity
1. Gap terlalu lebar
2. Speed root terlalu tinggi .
3. Amper root tinggi
4. Elektroda terlalu besar.
5. Khusus stainless steel root GTAW ditimpa diatasnya dengan GTAW pula sehingga root mencair lagi dan terhisap keatas oleh proses capillary .
Akibat dari cacat las ini adalah :
1. Mengawali erosi abrasi.
2. Menyebabkan S.C.C ( Cl2 , NAOH ).
3. Melemahkan sambungan .
Cara penanggulangannya yakni gouging sampai keakar yang bermasalah, stel ulang dan dilas sesuai WPS Repair.
Cacat las ini biasanya terjadi karena beberapa hal :
1. Gap terlalu lebar
2. Arus root terlalu tinggi
3. Mesin las tidak dikalibrasi dulu .
4. Elektroda terlalu dalam.
5. Speed root terlalu rendah .
6. Diameter elektroda terlalu kecil .
Akibat dari cacat las ini adalah :
1. Menyebabkan terjadinya notch yang berpotensi retak
2. Mengawali erosi abrasi.
3. Merusak pipe cleaning pigs.
Cara penanggulangannya yakni gouging hingga akar, kampuh dan stel ulang kemudian dilas menggunakan WPS Repair .
Root Cracks
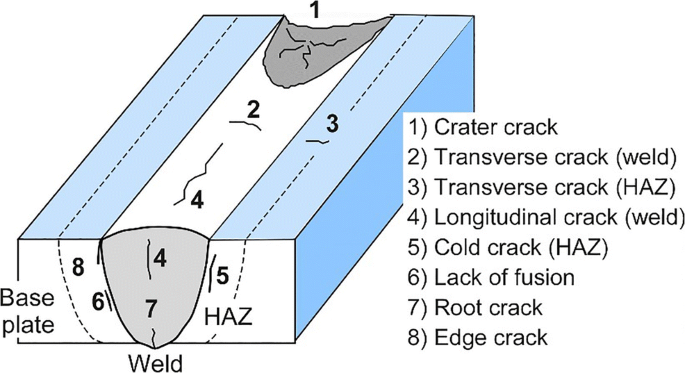
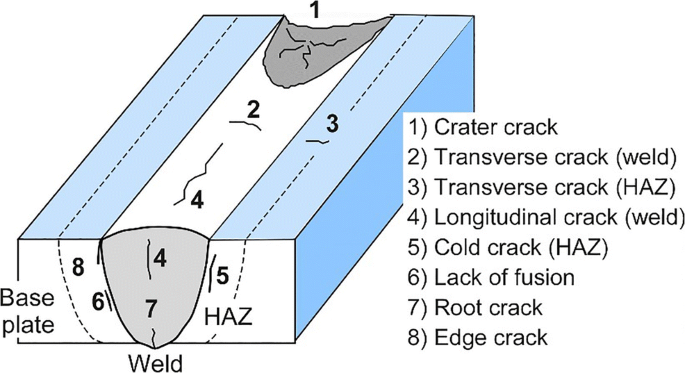
Cacat las ini biasanya terjadi karena beberapa hal :
1. Takik / notch
2. Tegangan ( stress )
3. C equivalent < 0.41 %
4. Penghilangan tegangan ( stress relief ).
5. Martensit di h.a.z
6. Pertumbuhan kristal ( crystal growth )
7. Kandungan ferrite < 5% dan > 12 % ( untuk stainless steel )
8. Ketidak sesuaian material ( reheat crack )
9. Stress Corrosion Cracking ( S.C.C ) ,Cl2 , C, H2 , caustic
10. Shrinkage ( pengkerutan )
Akibat dari cacat las ini adalah fatal.
Cara penanggulangannya yakni:
1. Diadakan analisa kegagalan ( failure analysis ) untuk mengetahui penyebab
retak secara akurat.
2. Jika retak berada didalam jalur las , digaouging , di kampuh ulang . distel dan dilas sesuai wps repair ( di
sesuaikan dengan hasil F.A )
3. Jika retak keluar kampuh, maka seluruh material ( base metal ) diganti baru, weld repair disesuaikan dengan hasil F.A.
Blow Hole / Burnt Through ( Terbakar Tembus )
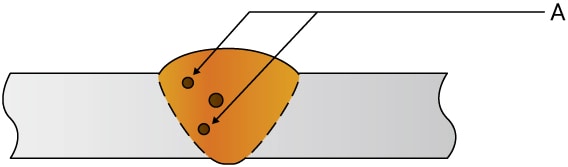
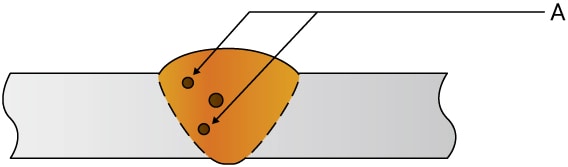
Cacat las ini biasanya terjadi karena beberapa hal :
1. Elektroda naik turun
2. Gap tidak konsisten
3. Amper root goyang / mendadak naik .
Akibat dari cacat las ini adalah menimbulkan S.C.C dilokasi cacat dan mengawali erosi abrasi
Cara penanggulangannya yakni Gouging sampai akar di lokasi cacat dan dilas isi sesuai WPS Repair.
Excess Wire ( pada GMAW atau FCAW )
1. Welding wire berkarat
2. Wire feeder tidak normal .
3. Pasokan listrik terputus putus
Akibat dari cacat las ini adalah :
1. Menimbulkan notch yang berpotensi retak.
2. Merusak cleaning pig
Cara penanggulangannya yakni gouging sampai keakar dilokasi cacat , dan dilas ulang sesuai WPS Repair.
Cacat las ini biasanya terjadi karena beberapa hal :
1. Gap kotor.
2. Amper root rendah
3. Suhu metal dingin
4. High Low.
Akibat dari cacat las ini adalah :
1. Menghasilkan notch yang berpotensi retak
2. Melemahkan sambungan
3. Mengawali erosi abrasi.
Cara penanggulangannya yakni gouging sampai keakar dilokasi cacat , dan dilas ulang sesuai WPS Repair.
Cacat las ini biasanya terjadi karena beberapa hal :
1. Gap terlalu sempit
2. Amper root rendah
3. Mesin las tidak dikalibrasi
4. Posisi elektroda naik turun
5. Gap kotor
Akibat dari cacat las ini adalah :
1. Timbul notch yang berpotensi retak
2. Menimbulkan S.C.C.
3. Melemahkan sambungan
4. Mengawali erosi abrasi
Cara penanggulangannya yakni gouging sampai keakar dilokasi cacat , dan dilas ulang sesuai WPS Repair.
Root Porosity
Cacat las ini biasanya terjadi karena beberapa hal :
1. Kondisi sebelah root lembab atau basah.
2. Elektroda lembab
3. Purging as terkontaminasi ( gtaw )
4. Tidak ada purging gas ( gtaw )
Akibat dari cacat las ini adalah :
1. Melemahkan sambungan
2. Mengawali erosi abrasi .
3. Mengawali internal corrosion.
Cara penanggulangannya yakni gouging sampai akar dilokasi cacat dan dilas ulang sesuai WPS Repair setelah kondisi pengelasan memungkinkan.
Cacat las ini biasanya terjadi karena beberapa hal :
1. Lingkungan yang basah atau lembab
2. Elektroda lembab
3. Angin masuk ke kolam las
4. Busur terlalu panjang
5. Arus Capping terlalu tinggi
6. Salah jenis arus
7. Salah jenis polaritas
8. Lapisan Galvaniiza belum digerinda
Akibat dari cacat las ini adalah buruk rupa dan mengawali karat permukaan. Cara penanggulangannya yakni cukup dengan dichip / pahat saja atau dikikir kasar, namun tidak boleh digerinda karena akan memakan permukaan base metalnya.
Cacat las ini biasanya terjadi karena beberapa hal :
1. Sudut bukaan kampuh terlalu besar
2. Elektroda terlalu kecil
3. Amper Capping tinggi
4. Lajur Capping belum selesai
5.Speed Capping terlalu tinggi
Akibat dari cacat las ini adalah :
1. Melemahkan sambungan
2. Mengawali karat permukaan
3. Timbul Displasment Stress ( tegangan geser ) yang berpotensi menimbulkan retak.
Cara penanggulangannya yakni langsung selesaikan lajur Capping sesuai WPS Asli.
Cacat las ini biasanya terjadi karena beberapa hal :
1. Terbentuk gas selama pengelasan seperti : CO2, CO, NO2, SO2
2. Udara merasuk kedalam kolam las.
Akibat dari cacat las ini adalah kemungkinan bocor sangat tinggi di lokasi cacat.
Cara penanggulangannya yakni cacat digouging hingga akar las , kemudian diisi las sesuai WPS Repair.
Cacat las ini biasanya terjadi karena beberapa hal:
1. Suhu metal rendah.
2. Amper capping rendah.
3. Ayunan ( sway ) tidak tetap
4. Permukaan bahan kotor.
Akibat dari cacat las ini adalah :
1. Terjadi incomplete fusion ( fusi tidak sempurna ) yang berpotensi retak.
2. Timbul kecurigaan bahwa seluruh lajur las dilaksanakan dengan amper rendah sehingga dapat meng akibatkan fusi antar bahan dasar dengan bahan las atau antar lajur tidak sempurna.
Cara penanggulangannya yakni :
1. Jika kecurigaan tidak terbukti, maka cold lap cukup digerinda saja sisi jalur uniform.
2. Jika kecurigaan terbukti maka seluruh jalur yang bermasalah dibongkar, dikampuh ulang dan dilas kembali sesuai WPS Asli. Juru las yang bermasalah diganti dengan yang lebih qualified ( baik ).
Cacat las ini biasanya terjadi karena beberapa hal :
1. Suhu metal terlalu tinggi.
2. Amper capping tinggi.
3. Speed capping terlalu rendah.
Akibat dari cacat las ini adalah :
1. Melemahkan sambungan .
2. Menghawali karat permukaan
3. Menimbulkan tegangan geser ( Displacement Stress ) yang berpotensi retak
Cara penanggulangannya yakni cukup membersihkannya dengan wire brush ( sikat kawat dan mengisinya dengan stringer ( pengelasan lajur tunggal tanpa digoyang ) sesuai WPS Repair.
Surface Underfill


Cacat las ini biasanya terjadi karena beberapa hal :
1. Suhu metal terlalu rendah.
2. Amper capping terlalu rendah.
3. Sisi kampuh kotor
4. Ayunan tidak sempurna
5. High Low ( penyetelan tinggi rendah )
Akibat dari cacat las ini adalah :
1. Timbul takik ( notch ) yang berpotensi retak
2. Melemahkan sambungan.
3. Mengawali karat permukaan.
Cara penanggulangannya yakni gerinda takiknya hingga sisa slag hilang, dan diisi stringer sesuai WPS Repair.
Cacat las ini biasanya terjadi karena beberapa hal :
1. Takik / notch
2. Tegangan ( stress )
3. C equivalent < 0.41 %
4. Penghilangan tegangan ( stress relief ).
5. Martensit di h.a.z
6. Pertumbuhan kristal ( crystal growth )
7. Kandungan ferrite < 5% dan > 12 % ( untuk stainless steel )
8. Ketidak sesuaian material ( reheat crack )
9. Stress Corrosion Cracking ( S.C.C ) ,Cl2 , C, H2 , caustic
10. Shrinkage (Pengkerutan)
Akibat dari cacat las ini adalah fatal.
Cara penanggulangannya yakni:
1. Diadakan analisa kegagalan ( failure analysis ) untuk mengetahui penyebab retak secara akurat.
2. Jika retak berada didalam jalur las , digaouging , di kampuh ulang . distel dan dilas sesuai WPS repair ( disesuaikan dengan hasil F.A )
3. Jjika retak keluar kampuh, maka seluruh material ( base metal ) diganti baru, weld repair disesuaikan dengan hasil F.A.
Cacat las ini biasanya terjadi karena beberapa hal :
1. Suhu metal rendah
2. Amper capping rendah
3. Speed capping rendah
4. Suhu lingkungan dingin
5. Busur terlalu pendek
Akibat dari cacat las ini adalah :
1. Timbul kecurigaan bahwa seluruh lajur dilas dengan amper rendah
2. Mungkin kondisi internal jalur las cukup baik namun perlu di selidiki lebih lanjut.
Cara penanggulangannya yakni:
1. Diadakan pengujian NDT baik dengan RT maupun UT ( straight atau angle probe ). jika hasilnya membuktikan bahwa kecurigaan benar , maka seluruh jalur yang bermasalah dibongkar dan dikampuh, distel dan dilas sesuai WPS Asli. juru las diganti yang qualified.
2. Jika hasil uji ndt menunjukkan kondisi internal jalur las baik , maka jalur menonjol cukup digerinda hingga uniform dan sesuai standard .
Cacat las ini biasanya terjadi karena beberapa hal :
1. Tonjolan berulang disebabkan oleh penggantian elektroda terlalu mundur sehingga terjadi overlapping yang menonjol.
2. Bagian yang kosong tanpa capping secara berulang disebabkan oleh penggantian elektroda yang terlalu maju.
Akibat dari cacat las ini adalah :
1. Yang menonjol tampak buruk dan tidak efisien.
2. Yang kosong menimbulkan notch yang berpotensi retak .
Cara penanggulangannya yakni :
1. Yang menonjol cukup digerinda kebentuk standard.
2. Yang kosong harus digerinda hingga sisa slag hilang, kemudian didisi las sesuai WPS Repair
Wide Bead
Cacat las ini biasanya terjadi karena beberapa hal :
1. Wide Bead yang bukan hasil manipulasi mutu :
a) Suhu metal relatif dingin
b) Ayunan terlalu melebar
c) Juru las tidak qualified.
2. Wide bead hasil manipulasi mutu.
a) Gap sangat lebar
b) Juru las dipaksa untuk mensiasatinya .
c) Gap disumpal dengan benda asing .
Akibat dari cacat las ini adalah :
1. Untuk Wide Bead yang bukan manipulasi mutu :
A) surface cold Lap kanan kiri Sisi las.
2. Untuk wide bead hasil manipulasi mutu :
A) Fatal, bahan dasar harus diganti.
Cara penanggulangannya yakni :
1. Gerinda cold lap sehingga lebar jalur las wajar.
2. Bahan induk ( base marial harus diganti baru ( jika ada ) , distel dan dilas ulang sesuai WPS Asli. Seluruh welding crew direject dan diganti ( karena telah memanipula si mutu secara kriminal ( tidak bertanggung jawab ).
Cacat las ini biasanya terjadi karena beberapa hal :
1. Salah penyetean
2. Beda Tebal
Akibat dari cacat las ini adalah :
1. Mengawali erosi abrasi .
2. Menghasilkan tegangan geser yang berpotensi retak.
Cara penanggulangannya yakni bagian yang menonjol diserong 1 : 3 ( ASME VIII )1 ; 2.5 ( ANSI B31.3 )
argon (Gas Tungsten Arc Welding)
Root Undercut
Cacat las ini biasanya terjadi karena beberapa hal :
1. Suhu metal terlalu tinggi
2. Amper root terlalu tinggi
3. Speed root terlalu rendah.
Akibat dari cacat las ini adalah :
1. Melemahkan sambungan dilokasi cacat
2. Mengawali erosi abrasi
3. Menimbulkan tegangan geser yang berpotensi retak
Cara penanggulangannya yakni gouging hingga akar, kampuh ulang , stel dan dilas sesuai WPS Repair
source:
pengelasan.net
operator-it.blogspot.com
LAS
untuk Definisi Pengelasan
untuk Pengelasan
untuk Jenis Pengelasan
untuk Proses Pengelasan
untuk Macam - Macam Elektroda/Kawat Las (Welding Electrode)
untuk Macam - Macam Cacat Las
untuk Kualifikasi Welder
untuk Tungsten Inert Gas (TIG) Welding / GTAW Argon (Gas Tungsten Arc Welding)
Root Undercut
Cacat las ini biasanya terjadi karena beberapa hal :
1. Suhu metal terlalu tinggi
2. Amper root terlalu tinggi
3. Speed root terlalu rendah.
Akibat dari cacat las ini adalah :
1. Melemahkan sambungan dilokasi cacat
2. Mengawali erosi abrasi
3. Menimbulkan tegangan geser yang berpotensi retak
Cara penanggulangannya yakni gouging hingga akar, kampuh ulang , stel dan dilas sesuai WPS Repair
source:
pengelasan.net
operator-it.blogspot.com
LAS
untuk Definisi Pengelasan
untuk Pengelasan
untuk Jenis Pengelasan
untuk Proses Pengelasan
untuk Macam - Macam Elektroda/Kawat Las (Welding Electrode)
untuk Macam - Macam Cacat Las
untuk Kualifikasi Welder
untuk Tungsten Inert Gas (TIG) Welding / GTAW Argon (Gas Tungsten Arc Welding)
Comments
Post a Comment