
Jenis Casting Defect / Cacat Casting
Berikut ini adalah jenis utama cacat pengecoran:
- Mismatch
- Swell
- Pinholes
- Blow holes
- Open holes
- Cut and washes
- Fusion
- Drops
- Metal penetration
- Shrinkage defect
- Run out
- Slag inclusion
- Hot or hard spot
- Hot tear or crack
- Col shut
- Dirt
- Misruns
- Honeycombing or Sponginess
- Fins and burns
- Warpage
1. Mismatch / Ketidakcocokan
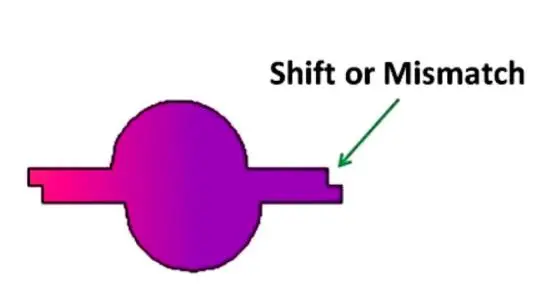
Mismacth dikenal sebagai pergeseran atau shift, ini adalah cacat pengecoran yang biasanya disebabkan oleh ketidaksejajaran bagian atas cetakan (cope) dan bagian bawah (dope). Kadang-kadang dapat terjadi karena ketidaksejajaran inti pada garis perpisahan.
Terutama ada dua jenis ketidakcocokan: pergeseran cetakan dan pergeseran inti. Pergeseran cetakan menunjukkan ketidaksejajaran cetakan dan sering terlihat sebagai perpindahan horizontal. Sedangkan pergeseran inti disebabkan oleh misalignment inti, yang muncul sebagai perpindahan vertikal.
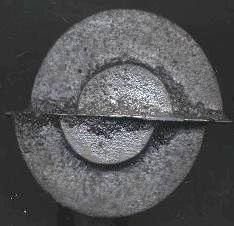
Penyebab
- Penjajaran bagian atas dan bawah yang tidak tepat selama proses cetakan.
- Disebabkan oleh pin kotak yang longgar dan pola pin dowel yang salah.
- Ketidaksejajaran flask
- Mengonfirmasi penjajaran dan pemasangan pola pelat pencocokan yang benar.
- Menggunakan kotak cetakan dan pin penutup yang tepat.
- Memeriksa keselarasan flask.
2. Swell / Membengkak
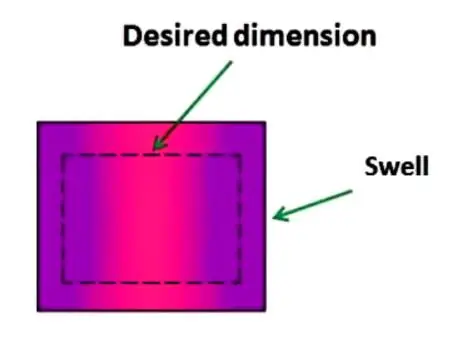
Swell mengacu pada pembesaran rongga cetakan. Hal ini disebabkan oleh tekanan logam cair, yang mengakibatkan pemanjangan produk pengecoran secara lokal atau keseluruhan. Biasanya berbentuk tonjolan kecil dan halus di permukaan pengecoran. Akibatnya, kebutuhan pengumpanan dan permesinannya akan meningkat, menghasilkan logam yang terbuang.
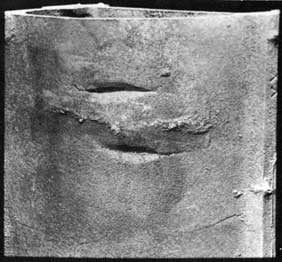
Penyebab
- Serudukan cetakan yang tidak tepat.
- Penggunaan cetakan berkekuatan rendah.
- Ini dapat dicegah dengan menggunakan cetakan yang kuat dan ditabrak dengan benar.
- Cetakan dirancang untuk menahan tekanan logam cair untuk mencegah gerakan dinding cetakan ke belakang.
3. Pinholes / Lubang kecil
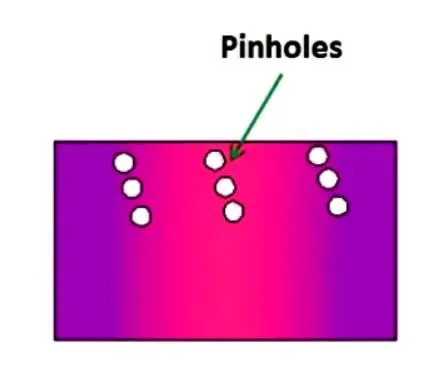
Pinholes juga merupakan cacat casting yang terjadi di bagian atas die-cast part. Ini adalah lubang kecil sekitar 2 mm, biasanya ditemukan di pocket berventilasi buruk di permukaan atas benda kerja.
Lubang-lubang ini terlihat jelas, artinya tidak diperlukan peralatan khusus untuk mengidentifikasinya. Umumnya, pinholes muncul dalam jumlah besar baik di atas casting atau tepat di bawah.
4. Blow Holes
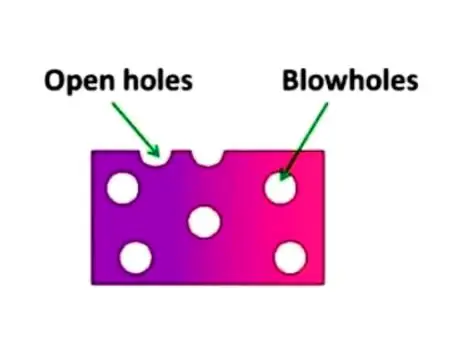
Blow holes adalah lubang besar yang terbentuk di dalam benda kerja cor. Lubang sembur terbentuk ketika gas yang terperangkap di permukaan pengecoran setelah mengeras membentuk rongga bulat atau oval. Lubang - lubang ini tidak terlihat dengan mata telanjang. Untuk mendeteksinya, diperlukan analisis sinar-X, ultrasonik, harmonik, atau magnetik.
Penyebab
- Pasir cetakan sangat lembap.
- Karena permeabilitas pasir yang rendah.
- Ventilasi yang buruk.
- Pasir cetakan harus memiliki kadar air yang terkontrol dan dijaga pada tingkat yang diinginkan.
- Pasir yang digunakan harus memiliki permeabilitas yang tinggi.
- Fasilitas ventilasi yang memadai harus disediakan.
5. Open Holes / Lubang Terbuka
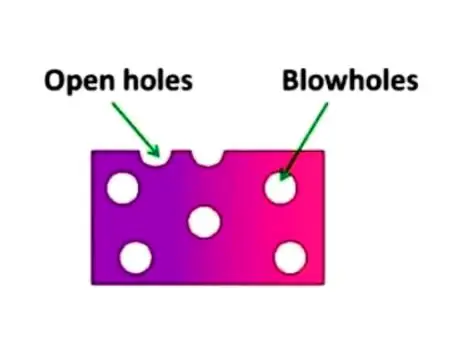
Ketika logam dituang ke dalam cetakan, lubang terbuka muncul di permukaan logam karena terperangkapnya udara. Cacat pengecoran jenis ini berbentuk bulat atau lonjong pada permukaan pengecoran. Seringkali memiliki permukaan yang halus dengan warna kuning atau putih cerah.
Setelah pengecoran, cacat ini dapat diidentifikasi sebagai cacat porositas gas dengan inspeksi visual. Selain itu, untuk memeriksa cacat ini pada permukaan non-mesin, diperlukan perangkat sinar-X.
Penyebab
- Ventilasi cetakan dan inti tidak memadai.
- Pengeringan cetakan dan inti yang buruk.
- Kelebihan kadar air pada pasir cetakan.
- Permeabilitas gas yang buruk dari pasir.
- Meningkatkan pemadatan dengan menurunkan suhu logam selama pengecoran.
- Keringkan cetakan dan inti sebelum digunakan dan simpan.
- Menggabungkan praktik fluxing dan melting yang baik.
- Meningkatkan permeabilitas cetakan dan inti.
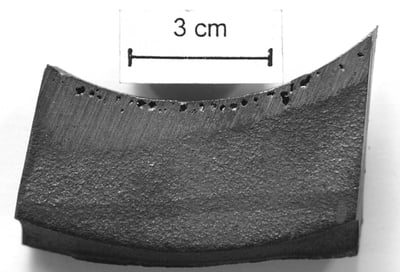
selajutnya... Casting Defect / Cacat Casting (part 2)
Comments
Post a Comment